CPS has been a longstanding partner of militaries around the world and their contractors. With applications ranging from radar to armor to munitions, the military and defense industry have turned to CPS to meet a variety of needs.
HybridTech Armor®
In 2012, CPS Technologies developed MMC encapsulated ceramic armor, called HybridTech ®, which is currently installed on U.S. Navy aircraft carriers. Additionally, CPS recently completed an SBIR to develop reconfigurable flooring systems for the UH-60 Black Hawk using HybridTech Armor®.
Benefits of HybridTech Armor® Compared to Legacy Solutions
High hard steel has historically been the material of choice for modern military defense applications that require heavy ballistic protection. While high hard steel provides exceptional hardness and ballistic protection, its density negatively impacts vehicle mobility, operational readiness, and total life cycle cost.
HybridTech Armor® offers a number of benefits, including:
- Size – HybridTech Armor® offers a thinner profile which optimizes the utilization of space within military vehicles and allows for more efficient integration of other systems and payloads.
- Weight – HybridTech Armor® provides a significant reduction in weight which improves mobility, fuel efficiency, and overall vehicle maneuverability to enable enhanced operational effectiveness in diverse terrains and combat scenarios.
- Performance – HybridTech Armor® exhibits enhanced ballistic resistance and protection capabilities thanks to the incorporation of MMCs which translates into superior survivability and increased defense against armor-piercing projectiles and explosive threats.
- Cost – HybridTech Armor® may involve a higher upfront investment, but it offers long-term lifecycle cost savings. The durability of MMC-based armor systems contributes to an extended lifespan, reduced maintenance requirements, and weight reduction which decreases logistical expenses.
While CPS is extremely proud of our work when it comes to protecting American soldiers, our work with the military goes beyond our armor.
Tungsten Warheads Made Using QuickSet™ Injection Molding
Tungsten (W) is an ideal metal for controlled fragment warheads. This is, in major part, due to its high density (19.25 g/cm3), allowing the same kinetic energy to be imparted in smaller fragments when compared to steel (8 g/cm3), allowing for less air resistance.
Unfortunately, tungsten is a very difficult metal to work with. With a high melting point (3,422oC) and the fact that tungsten, while strong, can be very brittle, casting and machining at high volumes is a difficult and costly endeavor. Using the QuickSet™ Injection Molding (QIM) can alleviate these problems.
QIM is a low-pressure powder injection molding process that produces parts with fine surface features at very high solids (>55 vol%). To accomplish this, QIM uses a colloidal metal or ceramic powder slurry for injection molding. The slurry is very fluid and can be modified for different powder material combinations for alloys and composites. Since the slurries are so fluid, accurate in-line process density measurements are used to provide feedback, which assures good dimensional control on the sintered final product.
By utilizing the CPS QuickSet™ Injection molding (QIM) process, tungsten and other difficult to use metals can be effectively manufactured at high volumes.
CPS Aerospace Applications
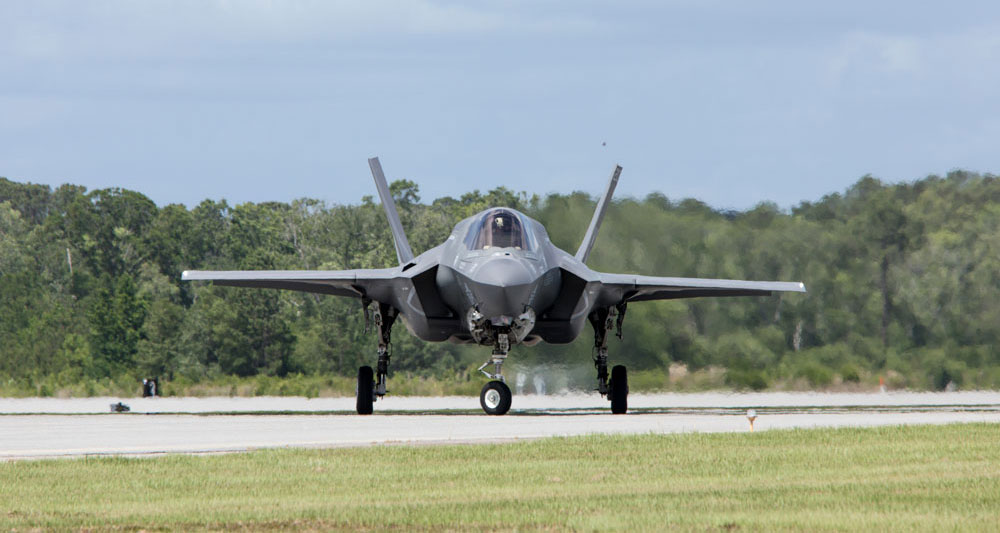
Ever since WWI, modern warfare cannot be discussed without talking about the skies. While historically this has meant planes and helicopters, it has quickly grown to also include space. Namely, satellites. Whether you are ten miles or 1,000 miles above sea level, CPS’ metal matrix composites and hermetic packages protect the reliability of electronic systems in a multitude of environments.
MMCs and hermetic packages like those developed by CPS offer advantages beneficial to the defense industry including:
- Excellent thermal conductivity – CPS metal matrix composites exhibit exceptional thermal conductivity. Effective heat dissipation enables efficient thermal management in high-temperature environments and improves the reliability of electronic systems and power devices.
- Low coefficient of thermal expansion (CTE) – In addition to excellent thermal conductivity, CPS MMCs provide a low CTE. This will limit the change in volume a material will go through due to changes in temperature. By utilizing different materials, CPS can allow our customers to hit a “sweet spot” in CTE, allowing our composite materials to be compatible with the materials our MMCs are designed to protect.
- High strength-to-weight ratio – CPS MMCs provide a high strength-to-weight ratio by combining lightweight materials like aluminum with reinforcing ceramic particles for increased strength while reducing overall density. By keeping weight in mind throughout the design process, we help our customers avoid the headache of trading off performance for weight savings.
- Long-term reliability – The lightweight and high-stiffness nature of AlSiC provides electronics with a substrate that is insensitive to shock and vibration, improving the long-term reliability of electronics subject to harsh vibrations. The aluminum of the AlSiC MMC is also corrosion resistant, improving electronics packaging where hermeticity is an environmental requirement.
“These four benefits are at the core of what makes CPS MMCs vital to our customers’ goals. By providing lightweight, durable products, our customers can feel at ease knowing their projects will operate at peak efficiency whether it be on Mars, the racetrack, at sea, and anywhere in between.”
Dr. Steve KachurVP of Technology at CPS
Global Innovation at CPS Technologies
Ready to discuss your MMC design needs?
CPS offers a suite of innovative solutions to give clients complete peace of mind in their solution. With our state-of-the-art AlSiC composite, proprietary machining processes, and time-tested expertise, we’ll show you why CPS is a trusted partner in the industry.
Trust CPS Technologies for Operational Success
Whether it be land, sea, or air, CPS Technologies has a proven record of designing, developing, and delivering cutting edge materials for military applications. Our team of material science experts is ready to overcome the next generation of challenges and meet your operational readiness needs.
Looking for a more modern material answer to traditional industry challenges? Discover the full potential of our MMCs by contacting CPS Technologies today for innovative solutions tailored to your needs.